A composite material is an assembly of at least two immiscible components (but with a high penetration capacity) whose properties complement each other. The new material thus constituted, heterogeneous, has properties that the components alone do not have.
To meet the ever more demanding needs of our customers, we have developed over the years the various composite manufacturing processes within our plants.
Contact molding or contact lamination is a completely manual process of shaping, at room temperature and without pressure

Contact manufacturing process
This is an easy method of implementation, with a relatively low molding cost. It makes it possible to obtain complex parts of very large dimensions.
Infusion is a modern process for the use of composite materials. It consists of vacuuming, in a mould closed by a tarpaulin, dry reinforcements which are then impregnated with the arrival of resin which is sucked in by the vacuum created in the mould
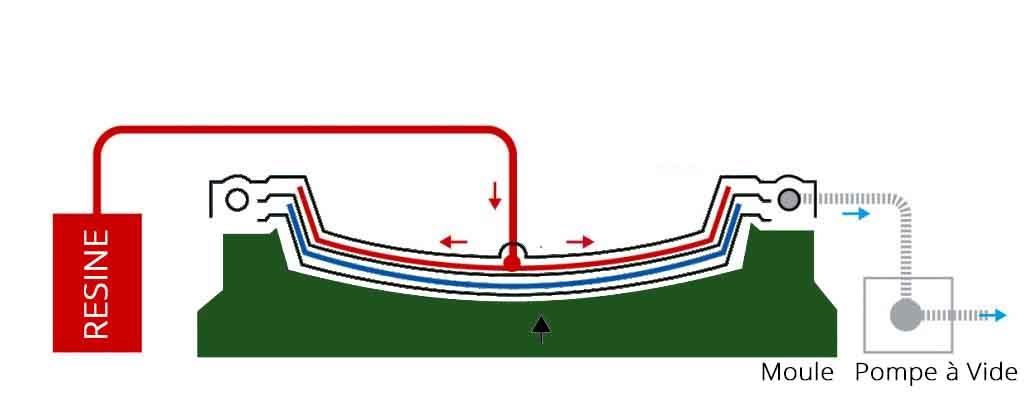
Manufacturing process Infusion
The advantages of infusion over contact moulding are:
- a higher fibre content and therefore better mechanical characteristics
- better repeatability in part production
- better protection of operators from solvent emissions
Low pressure resin injection molding is a technique for manufacturing composite material parts in a rigid and closed mold.
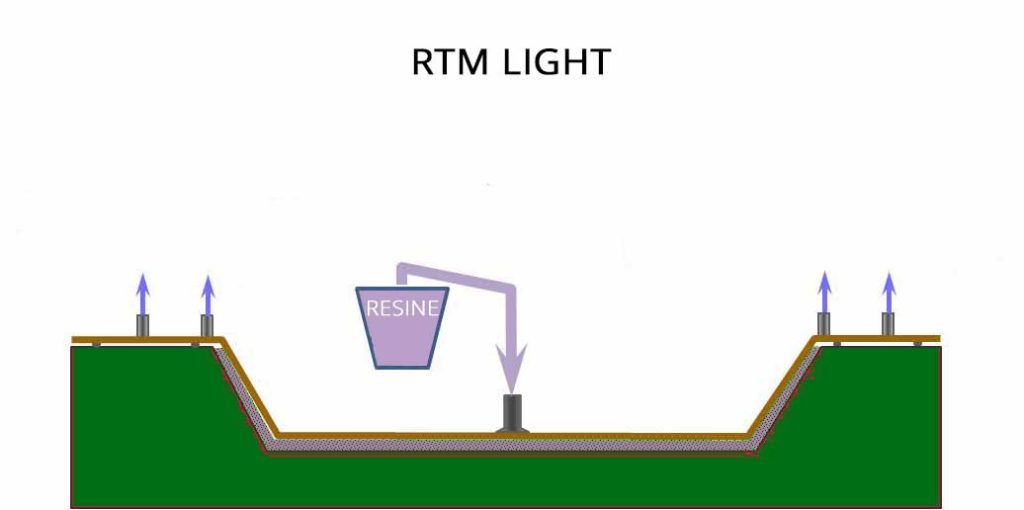
This process makes it possible to obtain composite parts with precise dimensions and a good surface finish. It is particularly suitable for medium and large series.
Le SMC (Sheet Molding Compound) est utilisé pour le moulage en compression où de plus hautes cadences de production sont exigées. La proportion de fibres de verre varie de 10% à 60%, avec une longueur de fibres supérieure à celle du BMC (BulkMolding Compound).
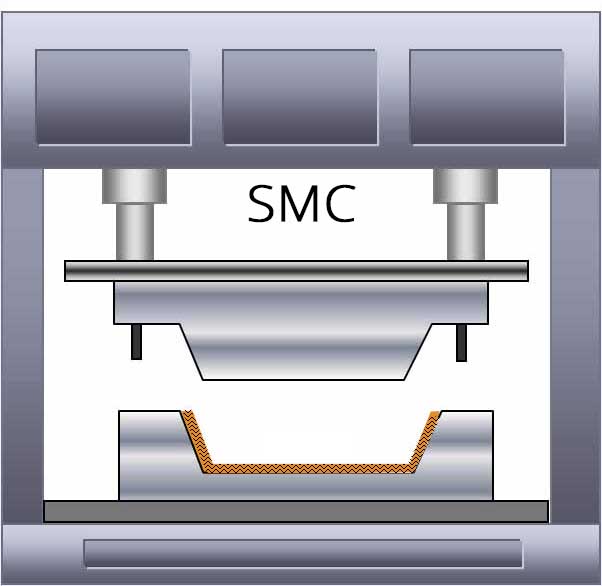
Le SMC est un mélange de résine, de charges, de fibres de renfort, de catalyseurs, de colorants et d’inhibiteurs, d’agents de démoulage et d’épaississants.
We produce parts tinted in the mass or ready to paint according to your needs.
We use the principle of late differentiation to meet your needs while minimizing the quantity of tools to be manufactured.
Our chain manufacturing sites for the application of different coating systems. Different aspects are then possible: matt, satin, gloss, smooth or textured, metallic or pearly. We are qualified for paint application in all our fields of activity.
Depending on the customer’s industrial needs, we deliver fully equipped plug & play solutions including the following activities:
- Bonding of windscreens and other glass products
- Bonding of floor coverings
- Installation of finishing joints for basins
- Installation of mechanical components
- Electrical connection
- Thermal and/or acoustic insulation installation
- Cold film application
- Functional tests
- Assembly kit preparations
From risk analysis from concept to product control bar: everything to ensure a stable manufacturing process and on-time delivery of parts.
From the development phase, we put customer satisfaction at the heart of the project in terms of cost, lead time and quality. Thus, the various processes are used to meet customer needs and improve the company’s performance.